اتصل
هاتف
+0086-371-86162511
عنوان
تشنغتشو ، الصين
wet ball mills similar

A method to identify wet ball mill’s load based on
In this paper, a novel method of wet ball mill load identification based on CEEMDAN, RCMDE and SRNN is proposed. Firstly, CEEMDAN-RCMDE is used to The difference between the result gotten from using wet and dry milling are most of the time very large. This difference is attributed to the power. The power to drive a wet ball mill is said to be 30% lesser than that of a Wet Ball Milling Vs Dry Ball Milling Orbis Machinery
احصل على السعر
Ball mill
A ball mill, a type of grinder, is a cylindrical device used in grinding (or mixing) materials like ores, chemicals, ceramic raw materials and paints. Ball mills rotate around a horizontal axis, partially filled with the material to be ground plus the grinding medium. Different materials are used as media, including ceramic balls, flint pebbles, and stainless steel balls. An internal cascading effect reduces the A numerical analysis of the impact energy distribution in the vessel showed that relatively high-impact energies of the balls were intensively generated near the Ball-impact energy analysis of wet tumbling mill using a
احصل على السعر
What Are the Differences Between Dry and Wet Ball Mills? How to
Advantages of wet ball mill: (1) The wet ball mill has better performance and higher grinding efficiency. It has low requirements for ore water content and can Ball milling is a simple, fast, cost-effective green technology with enormous potential. One of the most interesting applications of this technology in the field of cellulose is the preparation and the chemical modification of Ball milling: a green technology for the preparation and
احصل على السعر
Wet ball-milling synthesis of high performance sulfur
Wet ball-milling route is employed to prepare sulfur-carbon nanotubes composites. The influences of solvents, including ethanol and chloroform, on the A method for simulating the motion of balls in tumbling ball mill under wet condition is investigated. The simulation method is based on the three-dimensional Ball mill simulation in wet grinding using a tumbling mill and its
احصل على السعر
Grinding kinetics of quartz and chlorite in wet ball milling
For each grinding test, the mill was first loaded with a 1.86 kg mass of ball mix and a 150 g mass of feed sample material.A volume of 64.0 ml tap water was then added to the mill charge in order to make a 70 wt.% pulp density.Four mono-sized fractions of quartz and chlorite(− 2 + 1.19 mm, − 1.19 + 0.5 mm, − 0.5 + 0.25 mm, − 0.25 + 0.15 Ball mill plays a key role in mineral processing plant, and its load identification for optimal control has great significance for the energy consumption reduction and production efficiency improvement. The vibration signal of ball mill shell contains abundant load information, which can be used to identify ball mill load. However, due to the non-linear A method to identify wet ball mill's load based on CEEMDAN,
احصل على السعر
How can I determine the best RPM and balls to powder
Suppose after weighing the solvent you get 100 gm (solvent), now you can divide by 3 i.e., 33.3 gm of powder, 33.3 gm of solvent and 33.3 gm of grinding media...If you feel the quantiy of grindingThis study aims to investigate the ball milling effect on particles flotation using fractal dimension, in which the calculations in the particles morphology has been made using the step-length(PDF) Effect of wet ball milling on copper ore flotation by fractal
احصل على السعر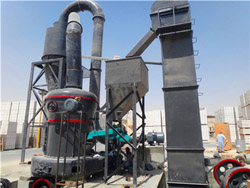
A comparative study on a newly designed ball mill and the
In continuous wet ball mills, the composition of feed (hard ore or soft ore) to the mill varies continuously, leading to uncontrolled grinding in the mill. In view of this, a new design of the discharge mechanism has been implemented to remove the ground particles of desired particle size fraction with minimum recirculating load (+150 µm).CERAMIC LINED BALL MILL. Ball Mills can be supplied with either ceramic or rubber linings for wet or dry grinding, for continuous or batch type operation, in sizes from 15″ x 21″ to 8′ x 12′. High density ceramic linings of uniform hardness male possible thinner linings and greater and more effective grinding volume.Ball Mills 911 Metallurgist
احصل على السعر
What Are the Differences between Dry and Wet Type Ball Mill?
The wet ball mill has a low noise, and low environmental pollution. The wet ball mill has a simple transportation device with less auxiliary equipment, so the investment is about 5%-10% lower than that of a dry ball mill. The grinding particle size is fine and uniform. The wet ball milling can not only grind agglomerate into fine particles, This review is focused on the topical developments in the synthesis of nanocomposites using the simplest top-down approach, mechanochemical milling, and the related aspects of the interfacial interactions. Milling constraints include time duration of milling, ball size, the ball-to-sample content proportion, rotation speed, and energy that Applied Sciences Free Full-Text Recent Developments on the
احصل على السعر
Wet ball-milling synthesis of high performance sulfur-based composite
The ball-milling was performed in a planetary ball mill (QM-3SP04, Nanjing) under ambient conditions at a speed of 300 rpm for 3 h. To investigate the influence of solvent, sulfur/carbon nanotubes composite are also prepared via same procedure by adding ethanol (10 mL, analytical) and chloroform (10 mL, analytical), respectively.Important advances have been made in the last 60 years or so in the modeling of ball mills using mathematical formulas and models. One approach that has gained popularity is the population balance model, in particular, when coupled to the specific breakage rate function. The paper demonstrates the application of this methodology to Optimization of Solids Concentration in Iron Ore Ball Milling
احصل على السعر
Continuous grinding in a small wet rod mill Part I. Comparison
Distribution of residence time data showed that flow through the rod mill was similar to that through the ball mill and the contents of the mill were The derivation of a mathematical model for breakage in a small continuous open circuit wet ball mill. Proc. A.I. Ch.E./I. Chem. E. Joint Meeting, London (1965) D.F. Kelsall et alBall mills find applications across many disciplines, from materials research to chemical analysis and even biological research [78,79,80]. Ball milling is a process that utilizes mechanical forces, such Producing Metal Powder from Machining Chips Using
احصل على السعر
A method to identify wet ball mill’s load based on CEEMDAN,
In this paper, a novel method of wet ball mill load identification based on CEEMDAN, RCMDE and SRNN is proposed. Firstly, CEEMDAN-RCMDE is used to extract the load features of the ball mill. Then, taking the advantage of SRNN's fast training speed and strong generalization ability, a mill load identification model based on SRNN is Powder Technology, 23 (1979) 169 -178 Elsevier Sequoia S.A., Lausanne Printed in the Netherlands A Comparison of Dry and Wet Grinding of a Quartzite Ground in a Small Batch Ball Mill M. A. BERUBE*, Y. BERUBE** and R. LE HOUILLIER*** Groupe de Recherche en Automatisation Appliquee a 1 Industrie iVinerale, Faculte de Science et A comparison of dry and wet grinding of a quartzite ground in a small
احصل على السعر
Ball mill simulation in wet grinding using a tumbling mill and its
Visualization of actual ball motion in wet milling. The mill used in this work was a tumbling ball mill made of stainless steel having 81-mm inner diameter and 110-mm length. Monosize steel balls of 10-mm diameter were used as grinding media. In order to visualize the motion of balls, one side of the mill lid was made of transparent acrylicThe effect of ball mill on the morphological and structural features of cellulose has been described by Okajima and co-workers. 20 They treated microcrystalline cellulose derived from cotton linters in a planetary ball mill at 200 rpm for 4–8 hours in dry and wet conditions with three solvents (water, toluene, 1-butanol).Ball milling: a green technology for the preparation and
احصل على السعر
Modeling of Bauxite Ore Wet Milling for the Improvement of
Size reduction is a necessary operation in mineral processing plants and provides the desired size for separation operations and the liberation of the valuable minerals present in ores. Estimations on energy consumption indicate that milling consumes more than 50 % of the total energy used in mining operations. Despite the fact that ball curve is the ball with diameter of 3 mm while larger media provided bi-modal curves. It is interesting to note that a mixture between balls of 3 mm and 5 mm leads to a final product very similar to the one that uses just 5 mm balls. Another interesting point is that cylinders presented a poor performance in the wet grinding of a planetary mill.Influence of Media Geometry on Wet Grinding of a Planetary Ball Mill
احصل على السعر
Influence of Media Geometry on Wet Grinding of a Planetary Ball Mill
Small balls lead to a higher milling energy and faster particle size reduction, while larger balls lead to a lower milling energy and slower particle size reduction. For example, in a mill with aThe effects of slurry pooling on ball milling have been investigated. •. Product fineness was found not to be a function of slurry pool volume. •. High ball filling J and slurry filling 1.0 ≤ U < 1.3 led to high production of fines. •. From a batch milling perspective, slurry pool is undesirable for effective grinding.Effects of slurry pool volume on milling efficiency ScienceDirect
احصل على السعر- الرماد المتطاير من الطوب اطلاق النار
- كسارة الحجر Harga kapasitas 300 طن مربى
- All Crushers Manufacturer In Tamil Nadu Tamil Nadu Companies Fo
- تكلفة الإنتاج في الهند
- الآلات في مناجم الفحم في ولاية كوينزلاند
- استخراج وتصنيع كربونات الكالسيوم
- batch type ball mills
- مخاطر معدات التعدين تحت الأرض
- آلة كسارة الحجر الرمال المحمولة صنع المحجر
- المستخدمة المحمولة كسارة الفك
- lose weight in coal mill peru cost
- آلة تعدين حجر الذهب العراق
- نيجيريا مطحنة الأسطوانة العمودية لمصنع الحديد
- الذهب عملية خط الصخور الفك كسارة
- asian grinding stone for sale