اتصل
هاتف
+0086-371-86162511
عنوان
تشنغتشو ، الصين
hardness of iron ore sinter

(PDF) Iron Ore Sintering: Quality Indices ResearchGate
Sinter plants process a mixture of iron ore fines, recycled ironmaking products, slag-forming agents and solid fuel (coke) with the Sintering is the most economic and widely used agglomeration process to prepare iron ore fines for blast furnace use. Compared with pellets, production of sinter Iron ore sintering ScienceDirect
احصل على السعر
(PDF) Microstructure and Minerals Evolution of Iron
The evolution of the microstructure and minerals in sinter showed that enhancing the Al2O3 content increased the proportion of Iron ore sintering is a high temperature process which converts iron ore fines (<6–8 mm in size, too small for direct feed into the blast furnace) into larger agglomerates containing bonding phases, Minerals Special Issue : Mineralogy of Iron Ore Sinters
احصل على السعر
Comprehensive evaluation of sintering basic
Sintering basic characteristics of fourteen iron ores were comprehensively evaluated using micro-sinter and grey relational analysis methods. The results show that The present study of the surfaces of sinter product and sinter returns has provided further evidence that the strength and breakage behaviours of iron ore sinters are dependent not only on the phases Minerals Free Full-Text Iron Ore Sinter Macro- and
احصل على السعر
Important iron ore characteristics and their impacts on
Until the 1950s of the last century, oxidized iron ores with a granulometry within 10 and 120 mm were loaded into the blast furnace (lower sizes led to permeability The basic characteristics refer to the high-temperature physicochemical properties of the iron ores, which reflects the iron ores behavior and function appearing in the sintering Comprehensive evaluation of sintering basic characteristics of iron
احصل على السعر
Modeling of degradation by impact of individual iron ore pellets
The approach that served as the basis for modeling pellets in the present work relies on the discrimination of the mechanisms of body and surface breakage during an impact event on a single iron ore pellet [4, 18].This approach accounts for the variability in the amenability of particles to undergo body breakage and on the fact that, when Chinese government data indicate that iron ore sinter producers will be able to save 0.42 million tons of standard coal [21] and cut CO 2 emissions per annum by approximately 1.16 million tons ifParticle size distribution of iron ores (wt-%). ResearchGate
احصل على السعر
Iron ore
Iron ores are rocks and minerals from which metallic iron can be economically extracted. The strength and hardness of iron increases with the concentration of phosphorus. 0.05% phosphorus in wrought iron To investigate the role of Al 2O 3 in iron ore sinters, constitutional analysis of high Al 2O 3 and low Al 2O 3 contained iron ore sinters was carried out by applying EPMA random sampling method.Effect of alumina and silica content in the calcium ResearchGate
احصل على السعر
Effect of Alumina on Calcium Ferrites Development in the Goethite Ore
The synthetic ore was used to make sinter mix by adding CaO, SiO 2, and Al 2 O 3 fluxes, while in the natural ores SiO 2 and CaO were added to adjust SiO 2 content to be above 4 wt pct and basicity (CaO/SiO 2) of all sinter mixes to be maintained at 1.87.The A 2 O 3 content in the sinter mixes prepared from each iron ore ranges from The effects of basicity and Al2O3 content on the chemistry of phases in iron ore sinter containing ZnO were investigated by Rietveld analysis of the X-ray diffraction (XRD) patterns. Bulk composition analysis was carried out using inductively coupled plasma-atomic emission spectroscopy (ICP-AES) and wet-chemical analysis. The composition of Effects of Basicity and Al2O3 Content on the Chemistry of
احصل على السعر
QUANTITATIVE XRD FOR ORE, SINTER, AND SLAG
Keywords: XRD, Rietveld method, data clustering, iron ore, sinter, slag, steel, DRI 1 INTRODUCTION The iron and steel making industry is responsible for a substantial percentage of anthropogenic CO2 emissions. Its contribution to the global warming impact is about 650 million tons of CO2 per year [1]. TheThe data of sinter pot show that the tumbling test index of sinter increases 2.94% and the RDI of sinter decreases 3.37% when added 15% A in production blended iron ore. View Show abstractThree-dimensional structure and micro-mechanical properties of iron ore
احصل على السعر
Effect of Iron Ore Pellet Size on Metallurgical Properties MDPI
Iron ore pellets are small and hard spherical particles agglomerated from a fine iron ore concentrate. They are used in the blast furnace process to produce hot metal. The diameter of blast furnace pellets is usually between 8 and 16 mm. In this study, a batch of magnesia iron ore pellets was first sieved into particle sizes of 8–10 mm, 10–12.7 Based on the particle size, iron ores are classified as iron ore fines (<10 mm) or iron ore lump (6.3–31.5 mm); iron ore fines are first processed in a sinter plant, while lump ores can be charged into the blast furnace (BF) directly. Iron ore lump is the lowest cost iron bearing material for the BF burden.Sinter Plant Operations: Raw Materials SpringerLink
احصل على السعر
Microstructure and Minerals Evolution of Iron Ore Sinter:
In fact, a major part of the iron ores consumed rely on imports. Australia, Brazil, Canada, South Africa, etc. are the main iron ore exporters, and the long-term data show that the iron ores imported by China have even exceeded 90% of the iron ores consumed [2]. However, the high utilization of imported iron ores has also given rise to someReferences (69) 6,7) Iron ore sintering is an agglomeration process of a mixture of ore fines mainly consisting of iron ores, fluxes and fuel, which produces sinters with suitable chemical and(PDF) Iron Ore Sintering: Quality Indices
احصل على السعر
Reduction of Iron Ore Pellets, Sinter, and Lump Ore under
There have been studies about the low-temperature reduction degradation characteristics of pellets, sinter, and lump ore, [] as well as the softening, shrinking, and melting reduction behavior of all charge materials or just part of them. [3-9]Even though some research has considered all iron-bearing materials (sinter, iron ore pellets, and SiO2 and Al2O3 are two important minerals that can affect the mechanical and metallurgical properties of sinter. This investigation systematically studied the influences of these minerals and revealed their functional mechanisms on sinter quality. Results showed that with an increasing Al2O3 content in sinter, the sintering indexes Microstructure and Minerals Evolution of Iron Ore Sinter:
احصل على السعر
Minerals Free Full-Text Research on the Preparation of Sinter
Sinter has been introduced into the composite burden of the COREX ironmaking process in China to lower the material cost, but the proportion is limited due to its poor low-temperature reduction degradation performance in the shaft furnace. This work dealt with the preparation of sinter for the COREX process by varying the MgO content 5.1 Procedural — Determination of apparent hardness 5.1.1 The tests shall be made in accordance with the requirements of 1S.0650”6-1, ISO 6507-1 or ISO 6508-1, but also with the additional requirements given in 5.1.2 to 5.1.5. 5.1.2 The hardness class to which a test piece belongs shall be determined by Vickers hardness testingIS 15703 (2006): Sintered metal materials, excluding hardmetals
احصل على السعر
The impact of goethitic ore types across the value chain
Powdery or dusty ores have goethite with an appreciable portion of goethite crystallites less than 0.01mm diameter. Goethitic ores can enhance sinter productivity. Fine ochreous goethite enhances granulation in sintering. Vitreous goethite does not granulate as well, due to smooth surfaces.Secondary hematite (SH) is a serious factor resulting in reduction degradation of iron ore sinter in a blast furnace; however, until now, a quantitative study for SH formation had not been reported. In this work, the effects of gangue composition, including MgO, Al2O3 and SiO2, on the solid-state formation in the sintering process of Minerals Free Full-Text Quantitative Investigation of MgO,
احصل على السعر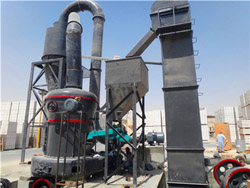
Increase in Low-temperature Reduction Degradation of Iron Ore Sinter
arising crack. Minerals in sinter are not so homo-geneous as ceramics, but indentation microfracture method was used to evaluate fracture toughness of minerals in sinter, since preliminary experiments showed a range of hardness 6N 7 (GNm-2), and that of fracture toughness 0.7-'1.6 (MNm-3/2), whichThe comprehensive hardness value and comprehensive fracture toughness value of vanadium-titanium sinter are both less than Through the 3D reconstruction of two types of iron ore sinters,(PDF) Influence of charcoal replacing coke on microstructure and
احصل على السعر- سنگ شکن خرد کن
- hammer mill control with pid controller
- ما هي المعدات اللازمة لتعدين الماس التجاري
- خطط بسيطة لبناء كسارة الفك الصغيرة
- السيراميك الصانع الكرة مطحنة في أمريكا
- jaw crusher in indiadolomite fillers application pdf
- معدات التعدين للكروم
- معدات تكسير الصخور pe 50
- آلة طحن عمودية التعدين
- jaw crushers for price in india for laboratories
- bapsfontein nombre de broyeurs
- البني لينوكس كوي كين الفك حجم محطم
- كسارة صخور الخبث الصلب
- how to make a granules from bentonite clay
- كسارة الخرسانة الصين للبيع